Understanding the Role of a High Pressure Die Casting Machine Manufacturer
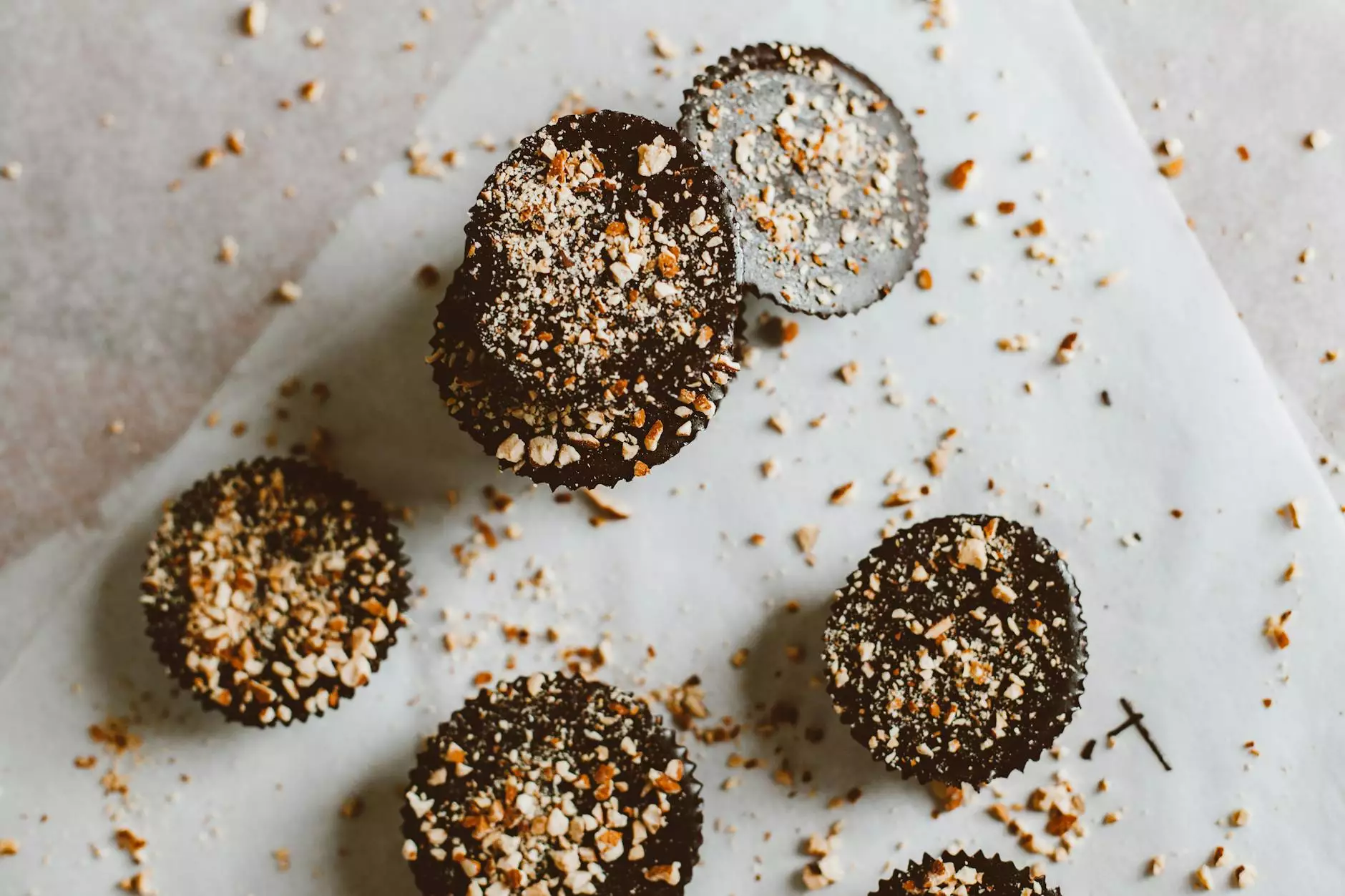
The manufacturing industry has undergone significant transformations with advancements in technology. One pivotal innovation is the development of the high pressure die casting machine, which is revolutionizing the way metal components are produced. In this article, we delve into the functionalities of these machines, the production process, their benefits, and why choosing the right manufacturer is crucial for businesses.
What is High Pressure Die Casting?
High pressure die casting (HPDC) is a highly efficient manufacturing process that involves the injection of molten metal into a mold cavity under high pressure. This technique is predominantly used for producing parts made of non-ferrous metals such as aluminum, zinc, and magnesium. The process is recognized for its ability to produce complex shapes with exceptional surface finishes and dimensional accuracy.
How High Pressure Die Casting Works
The operation of a high pressure die casting machine can be broken down into several critical steps:
- Preparation of the Mold: The mold is designed according to the specifications of the part required. It is usually made from steel to withstand the high temperatures and pressures involved in casting.
- Melting the Metal: The selected metal is melted in a furnace before being directed to the casting machine.
- Injection: Once the metal reaches the desired temperature, it is injected into the mold at high speed and pressure.
- Cooling: After the mold is filled, the metal is allowed to cool and solidify before the mold is opened.
- Ejection: The finished part is ejected from the mold, and the process can be repeated for additional parts.
The Advantages of High Pressure Die Casting
High pressure die casting machines offer numerous advantages that make them a preferred choice in manufacturing:
- Cost-Effectiveness: HPDC is highly efficient, allowing for faster production rates which result in lower labor costs and increased productivity.
- Precision and Accuracy: The process is known for producing parts with tight tolerances, ensuring that components fit perfectly in assembly.
- Complex Geometries: HPDC enables manufacturers to create intricate designs that would be hard to achieve with other manufacturing methods.
- Surface Finish: The resulting surface finish is often smooth, requiring minimal additional finishing work.
- Material Utilization: High pressure die casting minimizes waste, as excess metal can be reused in the process.
The Role of Deep Mould as a High Pressure Die Casting Machine Manufacturer
Deep Mould stands at the forefront of high pressure die casting technology, providing innovative solutions tailored to the needs of metal fabricators around the globe.
Tailored Machining Solutions
What sets Deep Mould apart is their commitment to providing customized die casting solutions. They understand that each project comes with its unique specifications and challenges. Their expertise in designing and manufacturing molds allows them to cater to diverse industries including automotive, aerospace, electronics, and consumer goods.
State-of-the-Art Technology
Deep Mould invests heavily in the latest technological advancements, ensuring that their high pressure die casting machines operate with the utmost efficiency. Utilizing cutting-edge software and robotics enhances the precision and speed of production.
Sustainability Commitment
In today's eco-conscious environment, Deep Mould prioritizes sustainability. Their machinery is designed to reduce scrap rates and optimize energy consumption, making them a responsible choice for manufacturers looking to lower their carbon footprint.
Why Choose Deep Mould?
There are several compelling reasons to select Deep Mould as your high pressure die casting machine manufacturer:
- Expertise: With years of experience in the industry, Deep Mould combines knowledge with practical skills to deliver outstanding products.
- Quality Assurance: They adhere to stringent quality standards, ensuring each machine meets both international and customer-specific requirements.
- Comprehensive Support: From initial design to post-sale support, Deep Mould offers a holistic approach to customer service, making them a partner in success.
- Competitive Pricing: Their commitment to offering cost-effective solutions does not compromise quality, making their machines an exceptional value.
Applications of High Pressure Die Casting
The versatility of high pressure die casting makes it applicable in various sectors:
Automotive Industry
The automotive industry is a principal consumer of high pressure die casting. Components such as engine blocks, transmission cases, and structural elements are commonly manufactured using this method due to the need for lightweight yet durable materials.
Aerospace Sector
In aerospace, where precision and safety are paramount, high pressure die casting is utilized for producing vital components that must meet rigorous standards while remaining lightweight.
Electronics
High pressure die casting is also prevalent in the electronics sector, particularly for enclosures and other parts requiring excellent finish and precise dimensions.
Consumer Goods
Consumer products, ranging from kitchen appliances to hardware tools, benefit from the efficiency and cost-effectiveness of HPDC, enabling manufacturers to produce reliable and aesthetically pleasing items.
Conclusion: The Future of High Pressure Die Casting
As technology continues to evolve, the landscape of metal fabrication and high pressure die casting is set for remarkable growth. Manufacturers must keep pace with the innovations brought on by leaders like Deep Mould. By embracing these advancements, companies can enhance their production capabilities, reduce costs, and meet the increasing demand for high-quality metallic components.
In summary, selecting a reputable high pressure die casting machine manufacturer is essential for success in the manufacturing landscape. With Deep Mould, businesses can trust in superior technology, tailored solutions, and unparalleled support to navigate the complexities of modern manufacturing with confidence.