The Pivotal Role of **Injection Plastic Mold Manufacturers** in Modern Industries
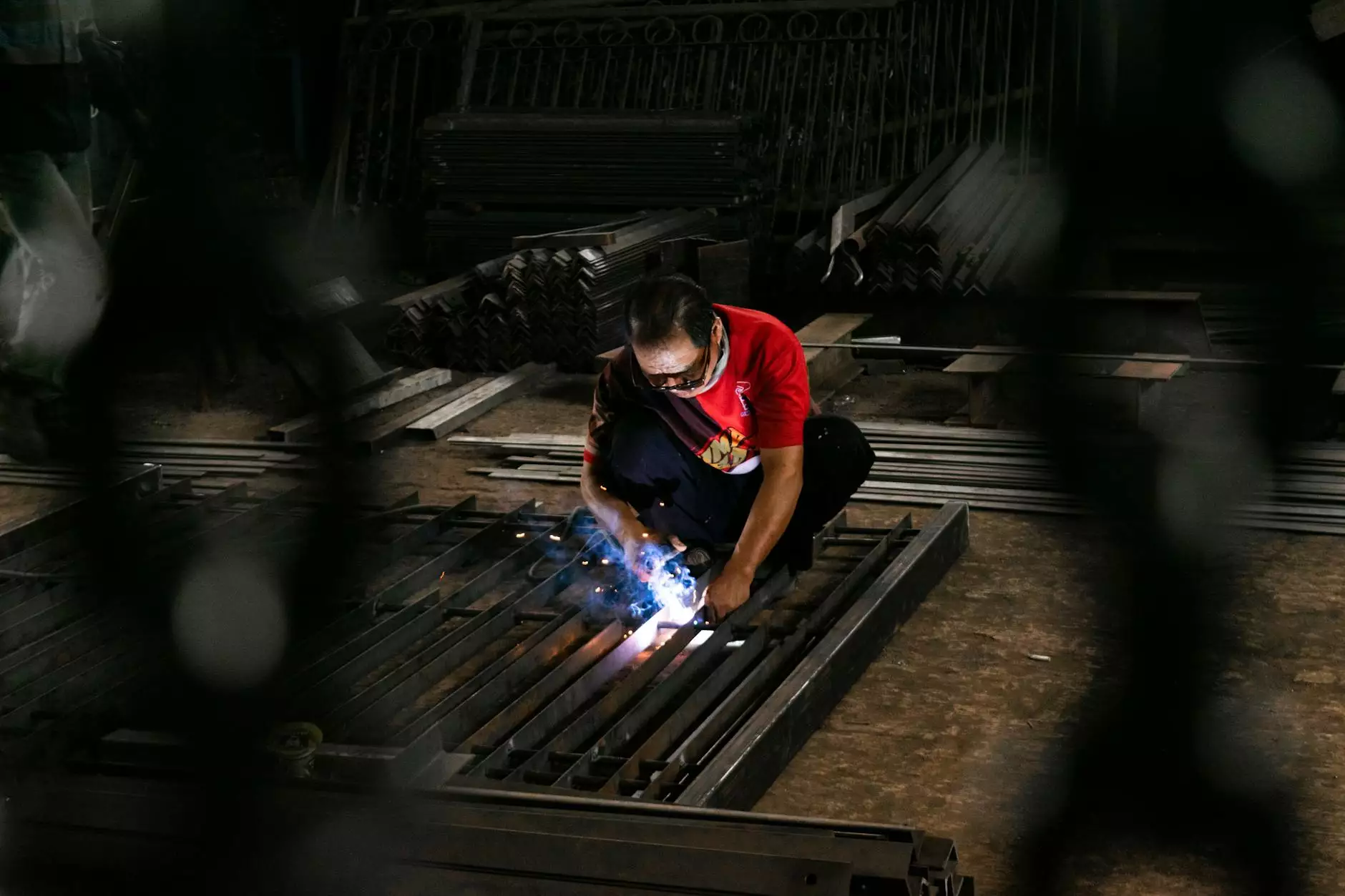
In today’s fast-paced manufacturing landscape, injection plastic mold manufacturers have emerged as indispensable partners for businesses seeking efficiency, innovation, and quality. Understanding the complexities of injection molding can significantly impact the capabilities and competitive edge of various industries, from automotive to consumer goods. This article delves into the mechanics of injection molding, the advantages of working with top manufacturers, and the intricacies of the metal fabrication process that underpins it.
Understanding Injection Molding
Injection molding is a manufacturing process that involves injecting molten material into a mold to create custom parts and products. This technique can be executed with various materials, but it is predominantly associated with plastics. The process is highly versatile, enabling manufacturers to produce a wide array of components efficiently and economically.
How Injection Molding Works
The injection molding process can be broken down into several key steps:
- Categorization of Materials: Selection of appropriate plastics or metal for the molds.
- Heating and Injection: The plastic is heated to a molten state and injected into the mold.
- Cooling: The injected material is allowed to cool and solidify within the mold.
- Demolding: Once cooled, the newly formed part is removed from the mold.
- Finishing Touches: Additional processes like trimming and surface finishing may be applied.
The Benefits of Partnering with Leading Injection Plastic Mold Manufacturers
Businesses can reap multiple advantages by carefully selecting their injection plastic mold manufacturers. These benefits can translate into significant cost savings and enhanced product quality.
1. Quality Assurance
Top manufacturers often have stringent quality control processes in place. They utilize advanced technology and adhere to international standards, ensuring each product meets the required specifications.
2. Cost-Effectiveness
By optimizing production procedures and reducing wastage, reputable manufacturers can offer competitively priced solutions without compromising on quality.
3. Technical Expertise
Partnering with experienced manufacturers grants businesses access to industry expertise, cutting-edge technologies, and innovative solutions tailored to their unique requirements.
4. Rapid Prototyping Capabilities
The best injection plastic mold manufacturers are adept at offering rapid prototyping services. This capability allows businesses to test and refine their products quickly before committing to full-scale production.
5. Flexibility and Customization
Every industry has unique needs. Leading manufacturers can customize their services to align with specific project requests, ensuring tailored solutions that cater to different sectors.
Factors to Consider When Choosing Injection Plastic Mold Manufacturers
While the advantages are clear, selecting the right manufacturer requires careful consideration of several factors:
1. Experience and Reputation
It's essential to evaluate a manufacturer’s history and reputation within the industry. Companies with a proven track record of reliability and excellence, like Deep Mould, should be prioritized.
2. Technological Advancements
The injection molding industry is continually evolving with technological advancements. Manufacturers who invest in the latest technology can often provide better quality and faster production rates.
3. Customer Support
Effective communication and strong customer support are critical in any business partnership. Ensure the manufacturer is responsive and willing to collaborate closely throughout the manufacturing process.
4. Portfolio of Services
A diverse range of services can be advantageous. Some manufacturers offer design assistance, prototyping, and post-production services, providing a one-stop solution for your manufacturing needs.
5. Certifications
When evaluating manufacturers, look for industry certifications that affirm their commitment to quality and safety, such as ISO certifications and compliance with industry-specific standards.
The Process of Metal Fabrication in Injection Molding
Metal fabrication plays a crucial supporting role in the injection molding process. It involves the creation of molds, tools, and fixtures needed to shape the injected materials accurately. Understanding this process is vital for anyone involved in manufacturing.
Steps Involved in Metal Fabrication for Molds
Metal fabrication encompasses a variety of operations, including cutting, bending, and assembling, all of which are essential in producing high-quality molds for injection molding.
- Design and Engineering: This initial stage involves creating detailed design specifications that meet precise measurements and functionality needs.
- Material Selection: Choosing the right materials for the mold, typically steel or aluminum, based on their durability and performance characteristics.
- Machining: The machining process transforms raw materials into components according to the design specifications through techniques like milling and turning.
- Assembly: Once all components are machined, they are assembled to form the final mold structure.
- Testing: The mold undergoes rigorous testing to ensure it meets all functional requirements and quality standards before being used in production.
Future Trends in Injection Plastic Mold Manufacturing
As technology continues to evolve, so too will the practices within injection plastic mold manufacturing. Here are some emerging trends that businesses should watch for:
1. Sustainable Manufacturing Practices
Increasing pressure for eco-friendly practices is driving manufacturers to explore sustainable materials and processes that reduce environmental impact.
2. Automation and Smart Manufacturing
Automation technologies, such as robotics and AI-driven processes, will enhance production efficiency and reduce human error, leading to improved consistency and quality in products.
3. Industry 4.0 Integration
The integration of IoT into manufacturing allows for real-time monitoring and predictive maintenance, optimizing production processes and reducing downtime.
4. Advancements in Materials Science
Innovations in materials science will lead to the development of new polymers and composites, enhancing the functionalities of the plastic molded products.
Conclusion: The Imperative of Choosing the Right Injection Plastic Mold Manufacturers
In conclusion, selecting the right injection plastic mold manufacturers can profoundly influence the quality, efficiency, and cost-effectiveness of your production processes. Thoroughly understanding the intricacies of injection molding and the metal fabrication techniques involved empowers businesses to make informed decisions, ensuring they engage with the most adept manufacturers in the industry. By partnering with experts who utilize cutting-edge technologies and maintain rigorous quality standards, companies can position themselves for success in a competitive marketplace.
Whether you are in the automotive, healthcare, or consumer goods sector, aligning with a reputable player like Deep Mould can dramatically enhance your manufacturing capabilities—delivering not just products, but innovations that drive your business forward.
© 2023 Deep Mould. All rights reserved.