Unveiling the World of Lathe Machining Parts Manufacturers
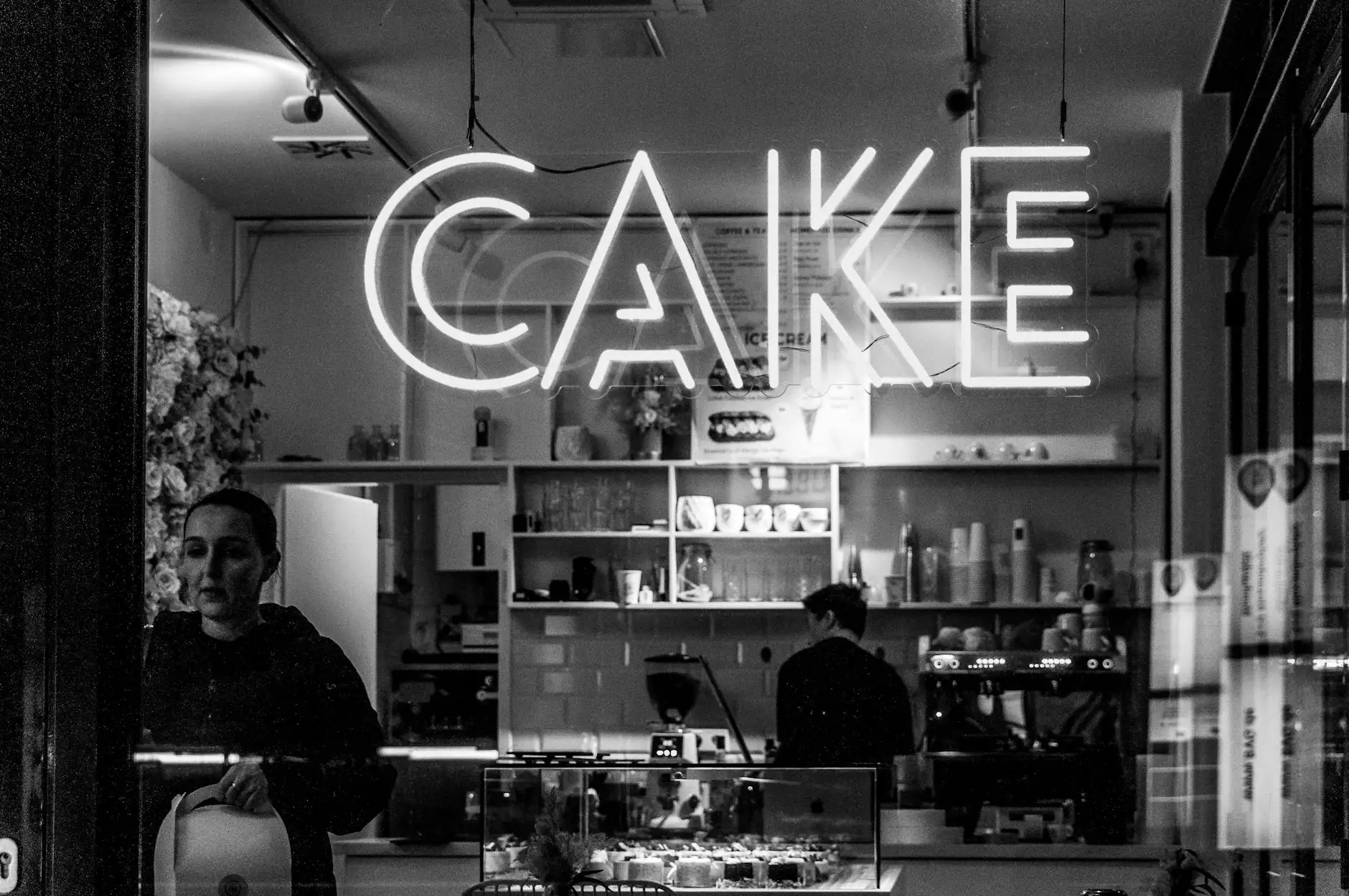
The realm of lathe machining parts manufacturers is pivotal to the success of various industries, including automotive, aerospace, and machinery. With a focus on precision, durability, and innovation, these manufacturers play a crucial role in shaping the components that make our modern world function efficiently. This article delves into the intricacies of lathe machining, highlighting its significance, processes, and the leading manufacturers in the field.
Understanding Lathe Machining
Lathe machining is a subtractive manufacturing process that involves rotating a workpiece against a cutting tool, which removes material to shape it into the desired form. This time-tested technique is renowned for its ability to produce high-precision components with complex geometries.
The Process of Lathe Machining
The process of lathe machining can be summarized in several key steps:
- Material Selection: Choosing the right material is essential for ensuring the durability and functionality of the final product.
- Setup: The workpiece must be securely mounted on the lathe to prevent movement during machining.
- Cutting Tool Adjustment: Proper alignment and setup of the cutting tools are crucial for effective machining.
- Machining Operations: Various machining operations, such as turning, facing, drilling, and threading, can be performed to achieve the desired dimensions and specifications.
- Quality Control: Rigorous inspection and testing ensure that the machined parts meet the required standards.
Importance of Quality in Machining Parts
In the metal fabrication industry, the importance of quality cannot be overstated. Parts produced by lathe machining parts manufacturers must adhere to stringent tolerances and specifications to ensure optimal performance in their applications. Here are the primary reasons why quality machining is vital:
- Performance: High-quality machined parts provide better performance and longevity in their applications.
- Safety: Faulty components can lead to safety issues, especially in industries like aerospace and automotive.
- Cost-Efficiency: Quality parts reduce the need for rework and replacements, translating to lower overall costs.
- Reputation: Manufacturers with a reputation for quality are more likely to be trusted by clients and partners.
Key Features of Lathe Machining Parts
When assessing the output of lathe machining parts manufacturers, consider these critical features that define superior lathe machined parts:
1. Precision Tolerances
The ability to maintain tight tolerances is a hallmark of reputable lathe machining. Tolerances define the allowable variations in dimensions, and high precision ensures that the parts fit perfectly in their intended applications.
2. Surface Finish
The quality of the surface finish impacts not just the aesthetic quality of the parts but also their performance. A smooth finish reduces friction and enhances durability, whereas a rough finish can lead to premature wear.
3. Material Compatibility
Different applications require different materials. Top-tier lathe machining parts manufacturers offer expertise in various materials, including metals like steel, aluminum, and brass, ensuring the right choice for every project.
Leading Lathe Machining Parts Manufacturers
With the growing demand for customized and precise components, numerous manufacturers have emerged as leaders in the field. Here are a few noteworthy examples:
1. DeepMould
DeepMould stands out for its commitment to quality and innovation in metal fabricators. Their advanced machinery and skilled workforce ensure the highest standards in lathe machining. Specializing in custom parts, they cater to various industries, ensuring that every client's specific needs are met.
2. XYZ Machining
XYZ Machining is known for its state-of-the-art CNC lathes that guarantee exceptional precision and repeatability. They serve clients in aerospace, automotive, and other critical sectors, providing tailored solutions that align with industry standards.
3. Global Lathe Solutions
Global Lathe Solutions emphasizes sustainable practices in their manufacturing processes while delivering high-quality lathe machining parts. They utilize advanced technologies to minimize waste without compromising on the quality of their products.
Technological Advancements in Lathe Machining
The landscape of lathe machining is constantly evolving, courtesy of technological advancements. Here are some significant trends shaping the future:
1. CNC Technology
Computer Numerical Control (CNC) technology has revolutionized lathe machining by allowing for automated machining processes with incredible precision. CNC lathes can perform complex operations with minimal human intervention, resulting in high productivity and consistent quality.
2. Smart Manufacturing
The integration of Internet of Things (IoT) technology into manufacturing processes enables real-time monitoring and data collection. This data can be analyzed to optimize machining processes, reducing errors and enhancing efficiency.
3. Advanced Materials
The development of new materials, including composites and alloys, presents new opportunities for lathe machining. These materials often exhibit superior strength-to-weight ratios and can be used to create lighter and more efficient components.
Challenges Faced by Lathe Machining Parts Manufacturers
Despite the numerous advantages, lathe machining parts manufacturers face several challenges:
1. Supply Chain Disruptions
Global events, such as the COVID-19 pandemic, have highlighted vulnerabilities in supply chains. Manufacturers must be adaptive and develop strategies to mitigate disruptions to maintain operations and customer satisfaction.
2. Skilled Labor Shortage
The demand for skilled labor in machining has outpaced supply. Manufacturers are investing in training programs to equip workers with the necessary skills to thrive in a technologically advanced environment.
3. Cost Management
Maintaining competitive pricing without sacrificing quality is an ongoing challenge. Manufacturers must streamline their processes to enhance efficiency and reduce costs while delivering superior products.
The Future of Lathe Machining Parts Manufacturing
The future of lathe machining parts manufacturing looks promising, driven by innovation and increasing demand for custom and precision-engineered components. Key factors influencing this future include:
1. Increased Demand for Customization
As industries lean toward personalized solutions, manufacturers must adapt by offering highly customizable products. This trend will require advanced machining capabilities and flexibility in production.
2. Sustainability Practices
With growing emphasis on environmental responsibility, manufacturers are adopting sustainable practices in their operations. This includes minimizing waste, optimizing resource use, and selecting eco-friendly materials.
3. Integration of AI and Automation
Artificial intelligence (AI) is making its way into production planning and quality control, leading to smarter manufacturing environments. Automation will enhance speed and efficiency while reducing human error in production processes.
Conclusion
In conclusion, the role of lathe machining parts manufacturers is pivotal in ensuring the success of various industries. Through advanced technologies, a commitment to quality, and an understanding of market needs, these manufacturers will continue to thrive in an ever-evolving landscape. As we move forward, embracing innovation and sustainability will define the future of lathe machining, driving progress and excellence in the field.
For anyone looking to partner with reliable and innovative manufacturers in the metal fabricator space, exploring options like DeepMould can yield fruitful results, paving the way for successful collaborations and superior product outcomes.