Understanding Automotive Plastic Parts: Innovations and Impacts
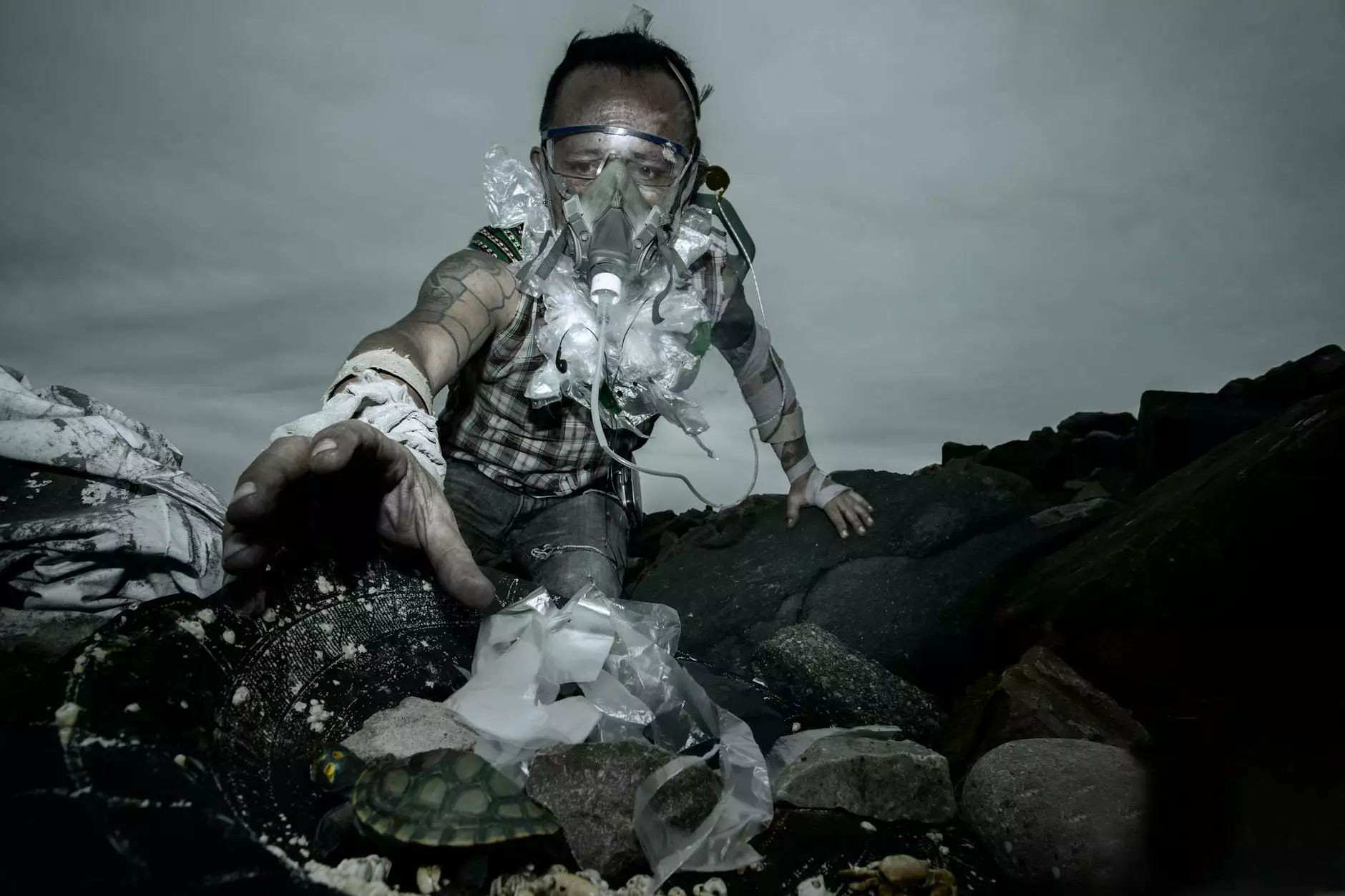
The automotive industry is undergoing a transformative phase, driven by innovation and the need for enhanced efficiency. One of the critical aspects of this transformation is the increasing adoption of automotive plastic parts. These components have become essential due to their lightweight, durable, and cost-effective properties, contributing significantly to vehicle performance and sustainability.
What Are Automotive Plastic Parts?
Automotive plastic parts are components made from various types of plastic materials used in the construction of vehicles. They range from exterior elements like bumpers and dashboards to interior components such as door panels and seat frames. The versatility of plastics allows manufacturers to design parts that can withstand the rigors of automotive use while also being aesthetic and lightweight.
The Importance of Automotive Plastic Parts
There are several reasons why automotive plastic parts are gaining prominence in vehicle manufacturing:
- Weight Reduction: Plastic parts often weigh significantly less than their metal counterparts, helping to reduce overall vehicle weight, which enhances fuel efficiency.
- Cost Efficiency: Manufacturing automotive plastic parts is generally less expensive than metal fabrication, reducing production costs.
- Corrosion Resistance: Plastics are naturally resistant to corrosion, which increases the lifespan of automotive components.
- Design Flexibility: Plastics allow for intricate designs that can improve aerodynamics and aesthetics.
- Safety Measures: Modern plastics can be engineered to enhance safety features, such as impact resistance and energy absorption.
Innovations in Automotive Plastic Parts
The design and production of automotive plastic parts have seen substantial innovations in recent years. Key advancements include:
1. Advanced Polymer Technologies
Manufacturers are now using advanced polymers to create parts that possess improved strength and durability. These polymers are designed to endure high temperatures and provide excellent performance under various conditions.
2. Sustainable Materials
With environmental concerns at the forefront, many companies are exploring bio-based plastics and recyclable materials. This shift not only helps reduce the carbon footprint but also aligns with consumer demands for eco-friendly products.
3. Enhanced Manufacturing Techniques
Innovations like 3D printing and injection molding have streamlined the production process of automotive plastic parts. These techniques allow for rapid prototyping and mass production, reducing lead times significantly.
The Role of Metal Fabricators in the Automotive Industry
While plastics dominate a significant portion of vehicle components, metal fabricators remain crucial in the automotive landscape. They produce metal parts that work in conjunction with plastics to create a balanced, well-functioning vehicle.
Why Metal Fabrication Matters
Metal fabricators like Deepmould.net play an indispensable role in providing quality metal components that complement automotive plastic parts.
- Structural Integrity: Metal components provide the structural integrity necessary for key vehicle functions.
- Safety: Metal parts contribute to the overall safety of vehicles, particularly in crash scenarios.
- Hybrid Structures: The combination of metal and plastic parts can lead to innovative hybrid structures that optimize performance and efficiency.
Case Studies: The Impact of Automotive Plastic Parts
To illustrate the impact of automotive plastic parts, consider the following case studies:
1. Weight Reduction in Sports Cars
Leading sports car manufacturers have incorporated automotive plastic parts to enhance speed and agility. By replacing metal with high-performance plastics in non-structural parts, these manufacturers achieve a significant overall weight reduction, which directly translates into better performance.
2. Cost-Effective Mass Production...
...In the production of compact vehicles, manufacturers have begun utilizing automotive plastic parts for external panels. This change has not only reduced costs due to lower material prices but also minimized the manufacturing time, allowing for faster turnover of new models to market.
Challenges and Solutions in Automotive Plastic Parts Production
While the advantages of automotive plastic parts are abundant, there are challenges that manufacturers face:
1. Material Degradation
Plastic can degrade over time due to exposure to UV light and environmental factors. However, the industry is addressing this challenge through the development of UV-resistant coatings and additives that enhance longevity.
2. Recycling Issues
Although many plastics are recyclable, the complex structures of automotive parts can hinder recycling efforts. The introduction of standardized materials and designs can facilitate easier recycling processes.
Future Trends in Automotive Plastic Parts
The future of automotive plastic parts is promising. As technology advances, we can expect:
- Smart Plastics: Integration of electronics into plastic parts for functionalities such as sensors and lighting.
- Higher Adoption of Sustainable Practices: Increasing emphasis on environmentally friendly production methods and materials.
- Continuous Improvement in Manufacturing Techniques: Innovations that reduce waste and enhance quality in production processes.
Conclusion
In conclusion, automotive plastic parts are revolutionizing the automotive industry by offering lightweight, durable, and cost-effective solutions. The collaboration between plastic manufacturers and metal fabricators like Deepmould.net will continue to push the boundaries of what is possible in vehicle design and production. As trends evolve, staying at the forefront of innovation will be vital for manufacturers looking to succeed in this competitive landscape.
By understanding the benefits and challenges of automotive plastic parts, stakeholders in the automotive industry can make informed decisions that lead to improved vehicle performance, safety, and sustainability.